易拉罐罐体用铝合金带材的技术开发
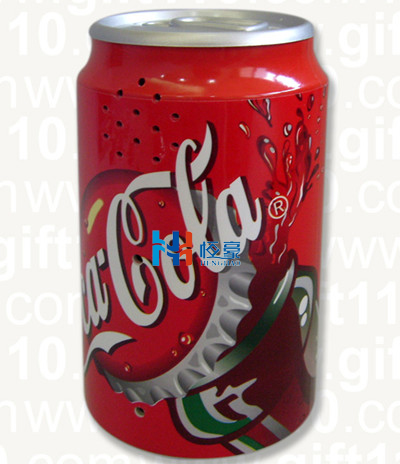
易拉罐的铝罐体生产要经过40多道工序,其中与铝带材性能相关的主要工序有落料、冲杯、变薄拉深、修边、冲洗、外印、内喷涂、烘干、缩颈、翻边等。铝带材必须具有适当的强度和良好的深冲成型性,以保证连续冲制、变薄拉深的顺利进行和烘烤后具有适当的屈服强度,目前罐体用铝合金仍然是A1一Mn系的AA3004、AA3104、AA3204 等合金铝带,状态为H19。
生产易拉罐的厂方对铝罐料的要求非常严格,不但要求内在质量好,化学成分优化,含气量、含渣量低,还要求有很好的深冲性能,制耳率要低,同时要求厚度公差小,板形好,有很好的表面质量,在易拉罐罐体的生产过程中,首先是将厚度为0.25 mill~0.30 HⅡn的带材冲落成直径为138 mm左右的圆料;然后经两次深冲制成冲杯,其直径减缩率大于50%;再经过三次变薄拉深,壁厚减到0.08 HⅡn~0.10 HⅡn,拉伸减薄率超过65%。由于变薄拉深加工可使坯料的延伸性处于极低状态,所以即使是很小的夹杂物也会成为破裂、折边的原因;随后,要保证在修边缩颈和翻边过程中不出现断裂,也要求材料具有较好的塑性;经过几次烘烤后,必须保证罐体的轴向承压和罐底耐压能力,要求罐体轴向承压1.35 kN,罐底耐压强度630 kPa,以确保罐装和储运顺利进行。因此,对罐体用铝带材的综合性能提出了相当严格的要求:抗拉强度270~310 MPa,屈服强度250~300 MPa,延伸率大于3% ,制耳率小于2% ;带材表面无明显波纹,表面光洁度均匀一致,无氧化,无肉眼可见的夹杂、压伤、斑痕等缺陷;带厚匀一致,厚差在0.005mm之内。
轻量化一直是易拉罐的发展趋势。随着制罐企业封缝机械和其它技术的不断进步,罐体用铝带材的厚度已由上世纪的0.343咖减为0.250 mm;罐盖用铝带材的厚度也由原来的0.39 HⅡn减为0.24 mm。为提高生产效率,各制罐厂家也在依靠先进技术不断提高罐体的成形速度,上世纪80年代中期,美国易拉罐生产线的生产能力都在800罐/min左右,而目前已达2 000罐/min。
为获得高质量坯料,从熔铸开始到热轧、冷轧、精整等各道工序都应严格控制。铸造时为了防止混入20~30p.m以上的夹杂物,须用SNIF法或陶瓷管过滤器对熔体进行过滤,并使用rri—B细化剂细化铸态组织。为了防止生成粗大化合物,细化剂的添加量须控制在最佳范围。罐体料的生产必须采用热轧供坯,最好采用热连轧,保证热轧后的温度在320 oC以上,再经过3~4道冷轧,厚度达到0.25~0.32 lnrn。冷轧后进行清洗、涂层、拉矫,在切边、重卷时进行静电涂油,然后包装出成品。热轧和冷轧时,重要的是控制带材的厚度、凸度、表面质量、力学性能及异向性等,制耳率规定在4% 以下。由于罐体坯料需要具有一定的强度和成形性,所以现在都采用3104一H19合金带材。表2所示是3104 一H19带材的典型性能。
铝罐的发展方向是薄壁化(即轻量化),以减少材料用量。350mL罐通常采用0.40—0.35n`l//l厚的带材,薄壁化后,带材厚度可减至0.32—0.25 n`l//l。单只铝罐的用料量已由1980年的12.93 g减少到10.71 g以下。
综上所述,随着生产技术的不断改进、易拉罐的轻量化和成形速率的提高,对铝带材的性能提出了更加严格的要求。只有不断地提高铝带材的精度、表面质量、内在冶金质量及成形性能,才能适应易拉罐的生产需要。